There are three giants in the electric car battery manufacturers in the world today: Panasonic, AESC and LG Chemical. Panasonic supplies Tesla, which is a joint venture between NEC and Nissan. Among the top 20 auto brands in the world, LG Chemicals has cooperated with 13 of them. Regardless of production capacity, LG Chemicals has become the world's “largest†supplier of automotive lithium batteries in terms of the number of cooperating manufacturers. So, what is the secret of LG Chemical's success: Relying on chemistry and materials science expertise, continuously reducing costs is the key to long-term success.
Prabhakar Patil, chief executive officer of LG Chemical Power Battery Division, said in an interview with foreign media that both Panasonic and AESC are consumer electronics companies. “LG Chemicals is the only battery company based on chemicals and materials. After decades of in-depth research, the establishment of ingredients and the development of chemicals, we have made each battery cell more stable and use core expertise to make battery technology progressive. The key factor for the development of batteries is the material and the acquisition of competitiveness is not only a matter of scale and material cost reduction, but also includes the improvement of material properties. LG Chemicals also takes care of it at the same time. Therefore, economies of scale have been formed."
In 2010, LG Chemicals made technical progress and contributed to the listing of the first Chevrolet Volt. At the time, LG Chemical Design was aiming for 40 miles (64 kilometers) of pure electric life, 200 Wh per mile, or 8 kWh. However, the actual installed first-generation battery capacity is 16 kWh. The 10-year service life is reduced by 30%, and the capacity window is only 70%. If the two factors are added together, 50% of the capacity will be obtained, and therefore 16 kWh becomes the rated capacity.
LG Chemicals has more than 400 engineers in South Korea's battery materials science. LG Chemicals hopes to improve battery capacity and longevity through better material engineering, as well as an effective capacity window without sacrificing battery performance. Patil expects that LG Chemicals will once again make a major technological breakthrough in 2017, which is faster than he had expected. “The US$30,000 and 200 miles (about 321 kilometers) of electric vehicles will become the mainstream of commercialization by 2017 or 2018. "Although General Motors has not confirmed whether the upcoming 2017 Chevrolet BOLT pure electric vehicles will use LG Chemical's batteries, it is generally believed that this will be the case.
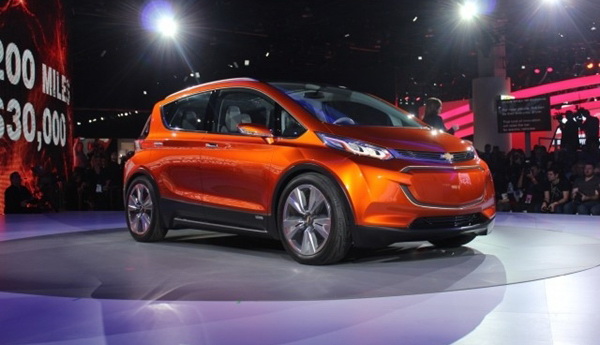
Chevrolet bolt pure electric car
Therefore, this is a battery-based technology and can be manufactured in large quantities without sacrificing quality and reliability. "We have more than 50 million batteries, more than 300,000 electric vehicles on the road, quality and reliability have reached the pharmaceutical-grade level, at the same time, there is no incident, which is very important for car manufacturers."
Patil said, "In a short period of time, the battery technology has been greatly improved. This situation surprised me." He cited the difference between the power and energy ratios in hybrid and electric vehicle batteries. "The battery for hybrid vehicles needs to be very high." High power, but not much energy, because of the regular cycle; batteries for electric vehicles must have enough energy to drive cars from 70 to 200 miles or more.†LG Chem has done both batteries, Patil stressed, made the ultimate power type Products and energy-type extreme products, the power and energy ratio difference may be 100 times larger. What LG Chem does is customize or optimize for specific applications, which is also one of the advantages of being a materials company.
How much time will it take for next-generation battery technology to surpass current lithium batteries? Patil said that the time will not be too long, the reason is simple, this is the basic chemical reaction, lithium is the third lightest element and the lightest metal. The only lighter than that is hydrogen, but it is difficult to control as a gas. If it is put into a pipe, it will be lost. If it is liquefied, it will lose its energy advantage. Therefore, lithium is the most suitable battery for Cai Lao. It can exist in some form for a long period of time. In the future it is possible to develop lithium metal batteries. Lithium is the most effective in both volume and energy efficiency.
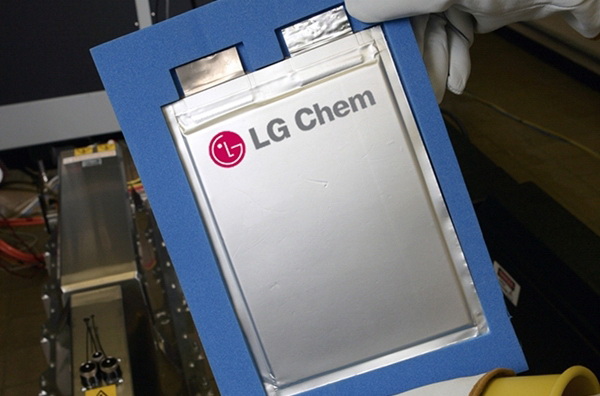
LG Chemical Battery
LG Chemicals is focusing most of its efforts on driving down costs. “If you look at the cost structure of the battery, manufacturing does not account for a large proportion. About 60% of the costs are related to materials. The material costs of battery manufacturers are mainly purchased materials, and are largely subject to scale and material performance characteristics. The impact. I think there is more to be done to reduce the net material cost, and by virtue of better design, customization, adjustment of properties, etc., the same excellent battery performance in Germany." Patil explained.
The current battery cost for most electric vehicles is about $400/kWh and Tesla is $240/kWh. Some commentators believe that the battery composition target of 125 US dollars / kWh, in order to match the cost of the internal combustion engine parity. Patil could not determine when this level could be reached. The first generation of Volenda had 288 batteries, and the second generation of Volenda had 192 batteries. LG Chemicals is promoting a large-capacity battery strategy to reduce the number of batteries by increasing the extra capacity of the batteries.
LG Chem supplies batteries to 13 brands including Volkswagen, Audi, Daimler, U.S. GM, Ford, Renault France and Hyundai. However, at present, AESC and Matsushita produce higher battery shipments than LG Chemicals. AESC will soon reach 200,000 units of Nissan Leaf, and its shipment volume will be more than double that of LG Chem. At the same time, Panasonic's battery capacity on each Tesla Model S is roughly three times that of the wind.
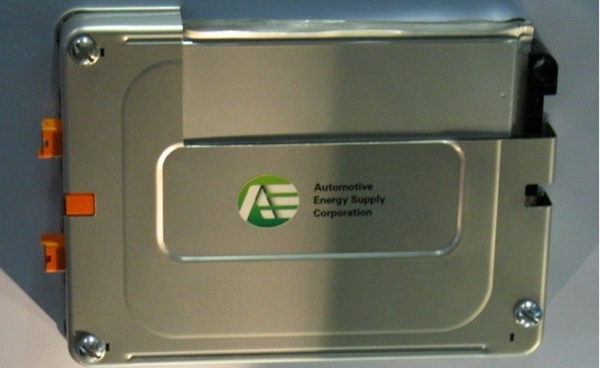
AESC lithium battery
On the other hand, Tesla and Nissan are relying on themselves, unlike most car makers who rely on suppliers to manufacture batteries. Nissan is actually one of the first companies to develop and manufacture lithium-ion batteries. They have a lot of internal strength. In the Nissan era, there was a hybrid battery pack, and the limited production used lithium-ion batteries that were developed in-house. However, I think that ultimately it all comes down to costs. Many executives are saying that even if they have internal capabilities, if someone can provide more Cost-effective solutions, we will purchase. Tesla is different, it is a more vertically integrated company, but it will also try to gain cost-effective internal and external forces." Patil said.
As early as April 2011, LG Chem announced that it had built the world's highest capacity battery plant in Ochong, South Korea, and recently added a factory in Michigan USA to supply Chevrolet Volenda and small-volume Chevrolet Spark EVs. battery.
Auto Parts Used For Joylong Hiace
Engine Hood,Joylong Hiace Car Door,Joylong Hiace Tailgate Rear Door,Joylong Hiace Engine Hood
Baoying Shuguang Auto parts Factory , https://www.shuguangautoparts.com